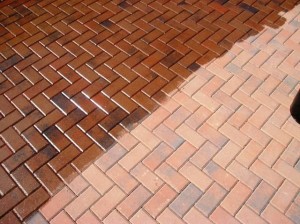
4 Easy steps to sealing interlocking pavers
Before sealing a paver project I always recommend that you let the pavers sit for one season or 6 months to allow the pavers to release efflorescence among other things. Always read the directions for the specific product you purchase as what I am presenting here is a general overview and each manufacturer has their own direction.
Sealers reduce the absorption of stains, oils and dirt into the paver surfaces. Application of a sealer should always follows stain removal, efflorescence removal and overall surface cleaning. Sealers are used for visual and functional reasons. They offer visual improvement by intensifying the paver colours. Some will add a glossy sheen or "wet look" to the pavers. Other sealers offer some colour enhancement and produce a low sheen, or a flat finish. Sealers offer many functional advantages, they can protect pavers from stain penetration. They are useful around trash receptacles, fast food restaurants, driveways, other areas subject to stains, and where oil drippings are not wanted . Sealers are also useful with limitations in stopping unwanted insects and weeds. Sealers can help maintain the sand in the joints under high velocity water flows. Where solvents may be spilled onto pavers, elastomeric urethanes and certain water based sealers have been successfully used to prevent their penetration.
The sealer manufacturer or supplier should be consulted prior to using any sealer to verify that their product will perform in the environment planned for its use.
Sealers can be either solvent or water based. Solvent based sealers consist of solids dissolved in a liquid. Solvent based products carry the dissolved solids as deep as the solvent will penetrate into the concrete paver. After the solvent evaporates, the sealer remains. Water based sealers are emulsions, or very small particles of the sealer dispersed in water. Water based sealers penetrate concrete as far as the size of the particles will permit. After the water evaporates, typically at a slower rate than solvents, the remaining particles bond with the concrete and to each other. These particles cannot penetrate as deeply as those carried by solvents. Water based sealer curing time will vary with the temperature, wind conditions and humidity.
Acrylics
Acrylic sealers can be solvent or water based. They enhance paver colours well and create a gloss on the surface. Acrylic sealers provide good stain resistance. Their durability depends on traffic, the quality of the acrylic and the percentage of solids content. They provide longer protection from surface wear than silanes or siloxanes. Acrylic sealants are widely used in residential and commercial paver applications. They generally last for a few years in these applications before re-coating is required. Acrylics specifically developed for concrete pavers do not yellow over time. When they become soiled or worn, pavers with acrylics can be easily cleaned and resealed without the use of extremely hazardous materials. Acrylics should not be used on high abrasion areas such as industrial pavements or floors. Water based acrylics perform well for interior applications. They may be allowed by municipalities that regulate the release of volatile organic contents (VOCs) in the atmosphere.
Urethanes
As either solvent or water based, polyurethanes produce a high gloss and enhance the colour of pavers. Aromatic urethanes should contain an ultra-violet (UV) inhibitor to reduce yellowing over time. The product label should state that the sealer is UV stable. Urethanes themselves are more resistant to chemicals than acrylics. While aliphatic urethanes can be used for coating the surface of pavers, elastomeric (aromatic or aliphatic) urethanes should be used where the primary need is to stabilize joint sand. Urethanes resist petroleum based products and de-icing chemicals. This makes them suitable for industrial areas. Urethanes cannot be rejuvenated simply by re-coating. If urethane sealers must be removed methylene chloride or sand blasting is often necessary. Methylene chloride is a hazardous chemical, and is not acceptable for flushing into storm drains. It should not be allowed to soak into the soil. Therefore, urethane removal is best handled by professionals.
Water Based Epoxy Sealers
Water based epoxy sealers combine other types of sealers with epoxy. They cure by chemical reaction as well as by evaporation. They have very fine solids allowing them to penetrate deep into concrete while still leaving a slight sheen to enhance the colour of the pavers. They generally do not change the skid resistance of the surface. When applied, water based epoxy sealers create an open surface matrix that allows the paver surface to breathe thereby reducing the risk of trapping efflorescence under the sealer should it rise to the surface. They resist most chemicals and degradation from UV radiation. These characteristics make these types of sealers suitable for high use areas such as theme parks and shopping malls. The elasticity and adhesion of these sealers make them appropriate for heavily trafficked street projects and areas subject to aggressive cleaning practices.
Sealing Procedures
All dirt, oil stains and efflorescence must be removed prior to sealing. The cleaned surface must be completely dry prior to applying most sealers. Allow at least 24 hours without moisture or surface dampness before application. The pavers may draw efflorescence to the surface, or the sealer or liquid stabilizer may whiten under any one of these conditions:
• The surface and joints are not dry
• The pavers have not had an adequate period of exposure to moisture
• There is a source of efflorescence under the pavers (i.e, in the sand, base, or soil) moving through the joint sand and/or pavers
• The sealer is not breathable, i.e., does not allow moisture to move through to the surface of the paver and evaporate.
If the base under the pavers drains poorly, the sealer is applied to saturated sand in the joints, or is applied too thick, the sealer can become cloudy and diminish the appearance of the pavers. In this situation, the sealer must be removed or re-dissolved. Consult your sealer supplier for advice on treating this situation.
Cover and protect all surfaces and vegetation around the area to be sealed.
For exterior (low-pressure) sprayed applications, the wind should be calm so that it does not cause an uneven application, or blow the sealer onto other surfaces. For many sealers, especially those with high VOC’s, wear protective clothing and mask recommended by the sealer manufacturer to protect the lungs and eyes.
Sealers can be applied with a hand foam roller for residential projects, and this is the recommended method for people who do not do this type of work all the time.
For larger areas, more efficient application methods include a powered roller. However, the use of a floor squeegee to spread the sealer will avoid pulling joint sand out of the joints.
Sealer should be spread and allowed to stand in the chamfers, soaking into the joints. Penetration into the joint sand should be at least 3/4 inch (20 mm). The excess sealer on the surface is pushed to an unsealed area with a rubber squeegee. The action of a squeegee wipes most of the sealer from the surface of the pavers while leaving some remaining in the chamfers to eventually soak into the joints. Generally only one coat is required.
For other applications, follow the sealer manufacturer’s recommendation for application and for the protective gear to be worn during the job. With some sealers that recommend two coats, the first coat usually applied to saturation. A light second coat, if needed, can be applied for a glossy finish.
Be careful not to over apply the sealers because the surface may becomes slippery when cured.
For water based sealers requiring two coats, always apply the second coat while the first coat is still very tacky. Prevent all traffic from entering the area until the sealer is completely dry, typically 24 hours.
If spraying sealer on the pavers, care should be taken to prevent the spray nozzle from clogging and causing large droplets to drop on the pavers. This is most important for water based sealers because it can cause a poor appearance and performance. Sealers normally require reapplication after a period of wear and weather. The period of reapplication will depend on the use, climate, and quality of the sealer.
Safety Considerations
Adequate slip and skid resistance of concrete pavers should be maintained with properly applied surface sealers. Federal, state/provincial, and some municipal governments regulate building materials with high volatile organic contents (VOCs). The restrictions usually apply to solvent based sealers. VOCs have been regulated since they can contribute to smog. Most water based sealers comply with VOC restrictions and some solvent based products may comply as well. The user should check with the sealer supplier to verify VOC compliance in those areas that have restrictions. Many solvent based products are combustible and emit hazardous fumes. Therefore, flame and sparks should be prevented in the area to be sealed. Never use solvent based sealers in poorly ventilated or confined areas. Persons applying sealers should wear breathing and eye protection as recommended by the manufacturer, as well as protective equipment mandated by local, state/provincial, or federal safety agencies.
Follow all label precautions and warnings concerning handling, storage, application, disposal of unused materials, and those required by all government agencies. The U.S. Federal Government and Canadian Government require that all shipments of hazardous materials by common carrier must be accompanied by a Material Safety Data Sheet (MSDS). All chemical manufacturers must supply sheets to shippers, distributors and dealers of cleaners and sealers if the materials are hazardous. The MSDS must accompany all shipments and be available to the purchaser on request. The MSDS lists the active ingredients, compatibility and incompatibility with other materials, safety precautions and an emergency telephone number if there is a problem in shipping, handling or use. The user should refer to the MSDS for this information.